
Mold Making & Urethane Casting
Rock Climbing Holds
Mosaic is Canada’s leading supplier of locally designed & manufactured rock climbing holds, sold world-wide through our online retail website Hold Emporium. Our holds are used in a vast array of settings such as:
Residential climbing walls
Commercial climbing gyms
Outdoor camp climbing walls
Commercial playgrounds
Entertainment & movie industries
We also offer production and fulfillment services to other climbing hold companies.
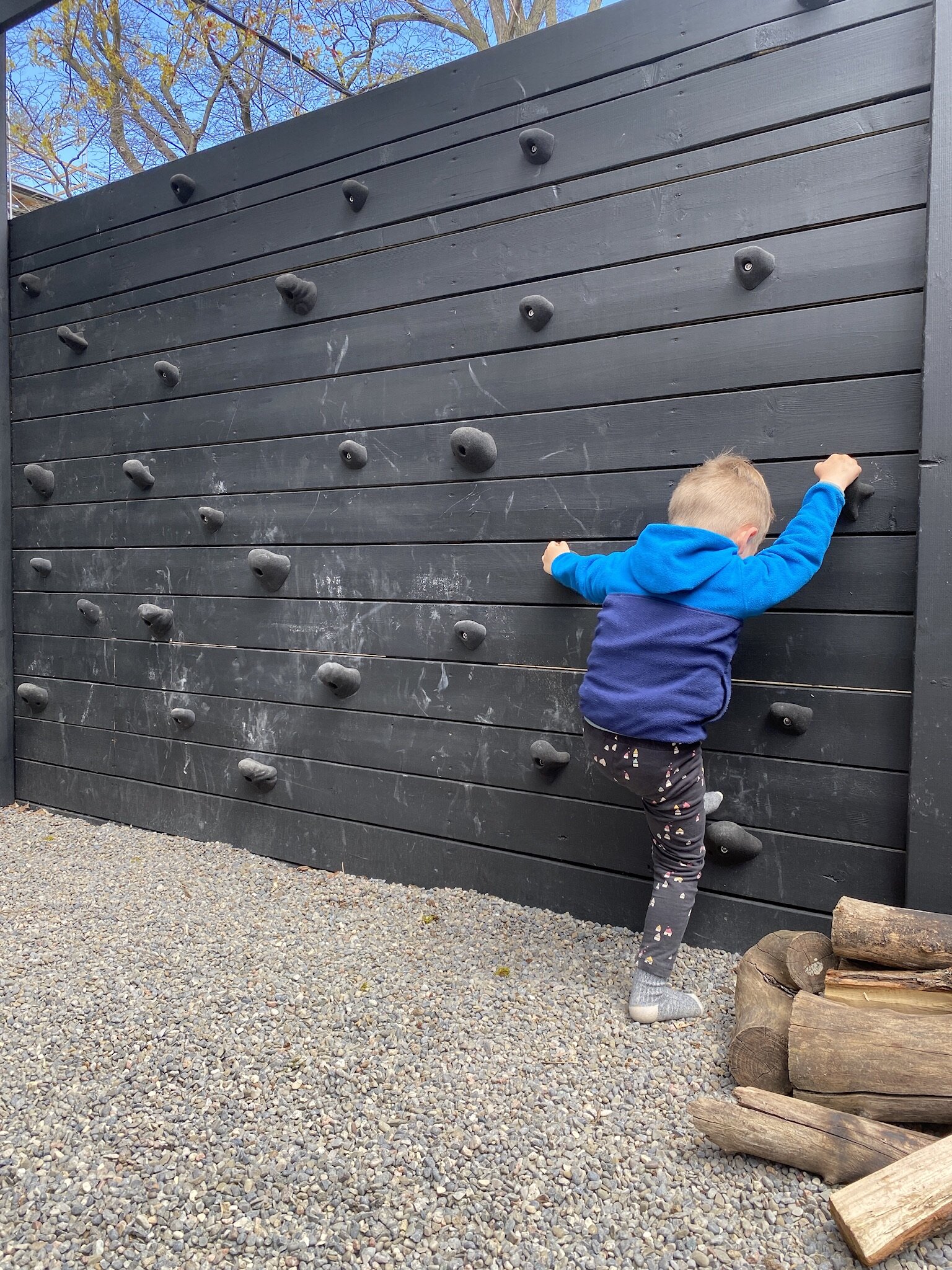
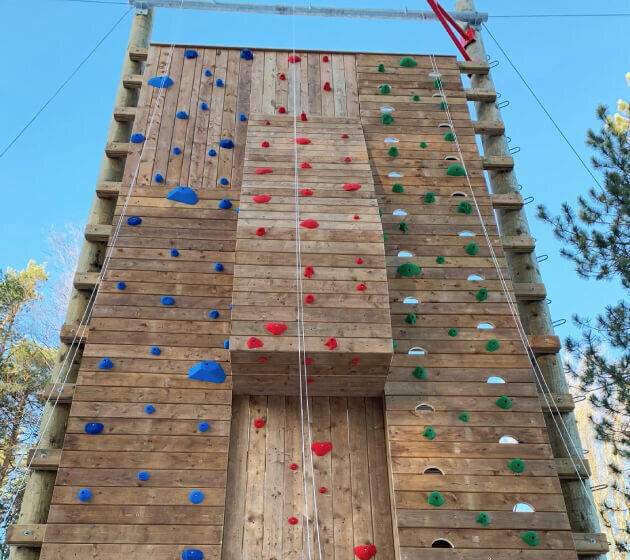
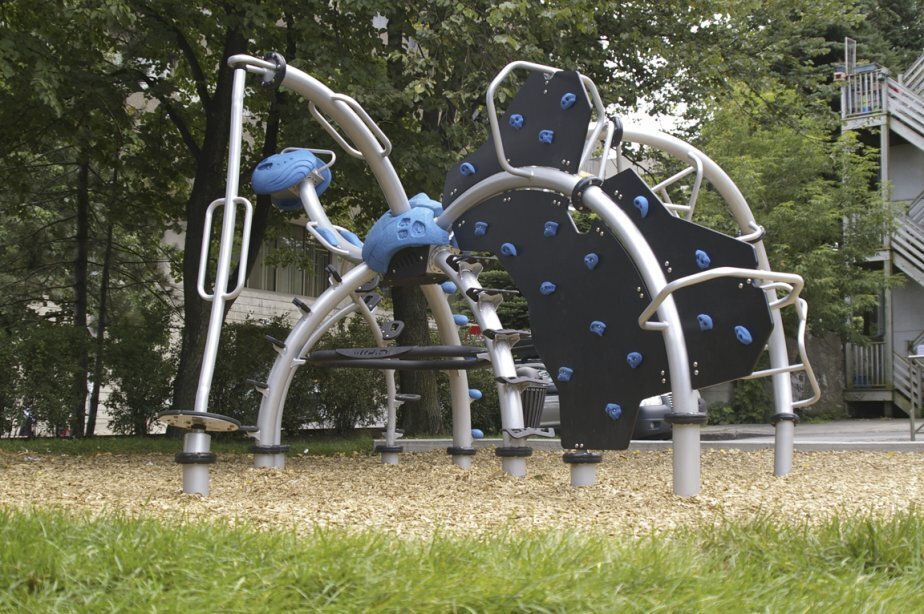




Our Process
Shaping
All of our climbing holds start from urethane sculpting foam. Our makers sculpt each shape with an idea in mind, focusing on the ergonomics and function of each hold. Holds can be shaped to replicate different rock textures or more child friendly shapes such as number, letters, animals, etc.
Molding & Production
Once a foam shape is made, it’s time to mold it for production. We decide on a molding method for each shape to ensure no materials are wasted. Larger shapes require a two-part mold to reduce the final cost and weight, while smaller shapes are molded together. When it comes time for production, we cast a durable polyurethane into the mold. Our plastic is custom formulated by a urethane chemist to withstand the stress that climbing holds must endure. It’s resistant to abrasion, cracking, and flexing, making it perfect for commercial and residential spaces. After the holds are cured, the backs of each hold are sanded flat and bolt holes drilled clean. Holds are then cleaned and checked for quality before packaging.
Most of our holds can be mounted using a ⅜” bolt on any climbing wall with t-nuts. Larger shapes will have screw holes that can be used as a second anchor point to stop holds from spinning. Some of our smaller shapes are mounted only using screws. All of our mounting points are poured with a metal washer to prevent holds from cracking.







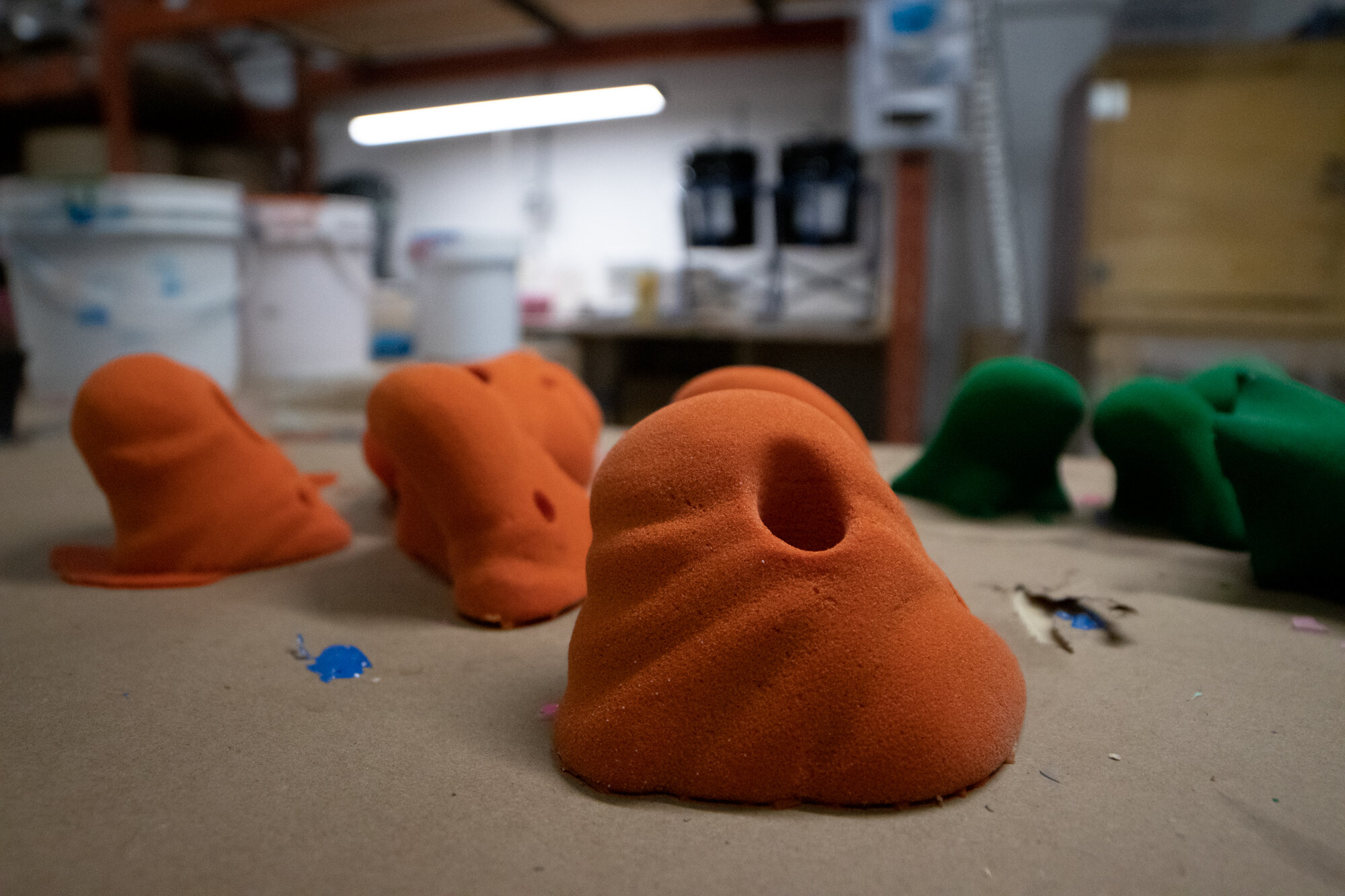